La loro strip di manovra brevettata, una fascetta in materiale plastico colorato che ricorda quelle da elettricista con la differenza che questa può essere aperta con una sola mano e riutilizzata all’infinito, ha rappresentato una rivoluzione per il mondo dell’auto.
Grazie alla sua adozione uno dei più importanti gruppi automobilistici europei, il cui nome è coperto da rigidi accordi di riservatezza, ha infatti ridotto da 5 a 1,5 minuti il tempo di stesura del cablaggio di un’auto e azzerato i danni occulti ai cavi degli impianti elettrici che derivavano dall’eliminazione del nastro di carta che li teneva in ordine durante la fase di trasporto.

Eppure C.B. – Costruzioni Brescianini, realtà milanese capace di imporre i propri standard in un settore dominato da grandi gruppi come quello dell’automotive, resta una piccola azienda con dieci dipendenti nel comune di Pogliano, a una decina di chilometri a Nord-Ovest del capoluogo lombardo. La sua caratteristica principale? Quella di riuscire a combattere contro multinazionali con migliaia di dipendenti e decine di stabilimenti in tutto il mondo puntando sulla velocità di reazione e sull’ingegno.
Nati a Milano nel cortile interno di una vecchia palazzina
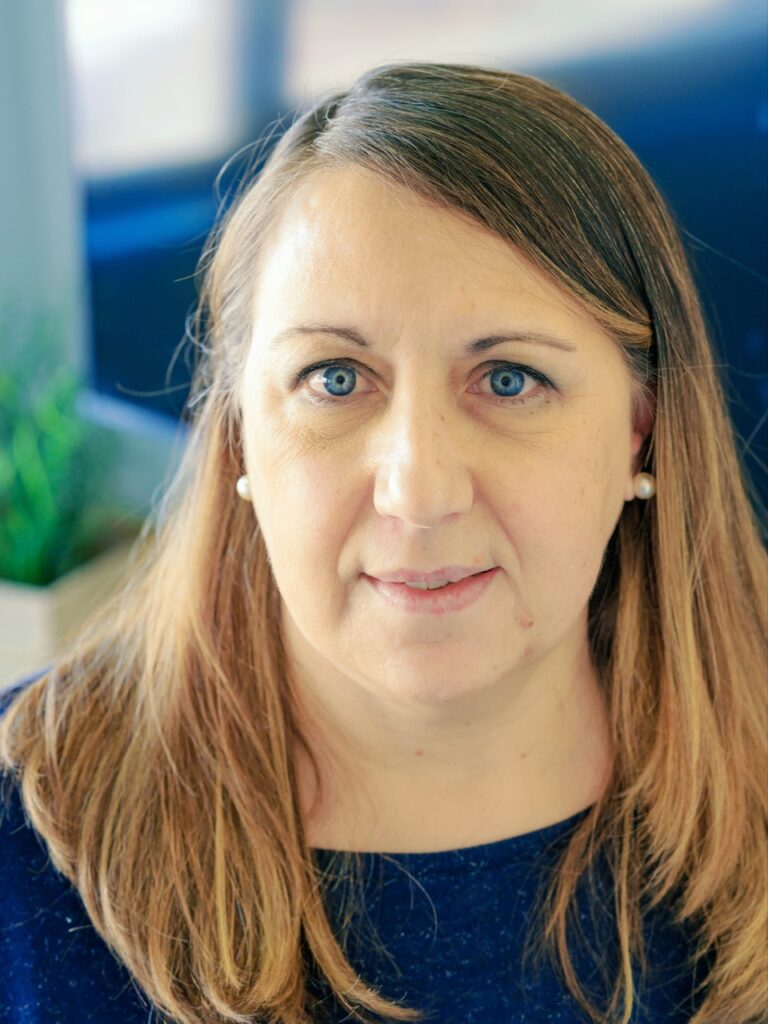
“La nostra azienda è nata nel 1986 a Milano, in uno dei tanti cortili interni della città in zona cimitero Monumentale”, racconta Clelia Petri, Responsabile controllo gestione e qualità dell’impresa fondata 35 anni fa da Davide Brescianini, attualmente amministratore delegato. “In una prima fase C.B. realizzava cablaggi per il settore automobilistico, ma dopo il trasferimento a Pogliano, all’inizio degli anni Novanta, ha aperto anche l’officina stampi e il reparto di stampaggio a iniezione”.
Lavorando per il settore automotive, Brescianini aveva infatti cominciato a cogliere una serie di piccole criticità lamentate dagli operatori del settore nelle fasi di trasporto e assemblaggio delle diverse parti. E, per rispondere a un’esigenza reale dei clienti, con passione aveva cominciato a immaginare e realizzare soluzioni in grado di migliorare notevolmente i processi. Se il primo esperimento fu la progettazione e produzione di un connettore per cavi elettrici che fosse migliore di quello che ai tempi era disponibile sul mercato, peraltro non sempre in tempi rapidi, nei decenni successivi le occasioni per esercitare ingegno e creatività sono diventate sempre più frequenti. Nascerà così la fascetta magica che elimina i difetti delle auto.
Obiettivo: risolvere problemi
“Laddove vedeva delle problematiche nelle linee di produzione, in qualche modo Brescianini si attivava per risolverle” conferma Petri, che con la sua passione e know-how ha contribuito a portare un approccio industriale in una realtà che resta artigiana. “Così sono nate una serie di soluzioni per il mondo dei cablaggi, di cui la nostra strip di manovra brevettata è solo l’esempio più eclatante”.
Oltre a velocizzare notevolmente i processi produttivi, questa semplice fascetta colorata – brevettata nel 2003 e utilizzata su larghissima scala a partire dal 2014 – ha consentito di eliminare la maggior parte dei difetti che si avevano sul cablaggio di un’auto. E ha reso di fatto più affidabili milioni di veicoli in circolazione sulle strade di tutto il mondo.
Lo scarto zero e le sfide dall’industria automotive
D’altra parte, il miglioramento dei processi e dell’affidabilità è alla base dell’approccio dell’azienda meneghina, che è associata ad A.P.I., l’Associazione Piccole e Medie Industrie. Lo dimostra un altro prodotto brevettato da C.B., un copri-polo universale per i diversi tipi di alternatore montati sulle auto, che ha azzerato il tempo e i costi della gestione dell’accoppiamento tra i vari modelli e il loro copri-polo dedicato. Oggi un unico copri-polo è utilizzato per tutti i diversi tipi di alternatore.
Ma c’è di più. Oltre al settore dell’automotive, che viaggia a scarto zero e che quindi richiede un livello di accuratezza e affidabilità assoluto su forniture che spesso sono fatte da milioni di pezzi, C.B. lavora per altri comparti. Da quello della produzione di bombole di gas, con la realizzazione di fondelli su misura per i contenitori in metallo e di beccucci anti-spreco per l’erogazione, a quello elettrico. Da quello medicale a quello aeronautico.

Dalla progettazione alla fase di stampa
“I nostri prodotti vengono tutti progettati, prototipati e poi stampati da noi”, sottolinea Davide Brescianini “cosa che ci consente di riassumere in un’unica visione le esigenze che derivano dalle diverse prospettive”. Sarà anche per questa peculiarità che sono richiesti in ogni angolo del pianeta.
“Esportiamo l’80% della produzione verso i mercati del Nord Africa, del Far East, verso i Paesi dell’Est, verso il Brasile e verso gli Stati Uniti”, conferma Petri. “E, anche in un anno disastroso per il settore dell’auto come il 2020, siamo riusciti a contenere i danni competendo in altri settori grazie al valore aggiunto delle nostre produzioni”.
Libero, 17 aprile 2021 (ultima modifica 20 aprile)
Leggi le storie degli altri Geni Lombardi